The automotive industry is interconnected and global. That is not going to change, with or without the presence of tariffs. Auto manufacturers in North America rely on parts, subassemblies, transmissions, semiconductor chips, as well as software, rare earth metals, and other metals like aluminum and steel from Canada, Mexico, Europe, China, Japan, and elsewhere. Tariffs will impact vehicles assembled in the US just as they will affect vehicles imported from other countries. It is possible for sourcing strategies and production locations to shift, but this takes years. As a 25% tariff by the U.S. on imports from Japan and other countries looms in response to a perceived uneven trade playing field, automotive OEMs (Original Equipment Manufacturers) and suppliers are strengthening connections with customers and partners across the supply chain, as well as with the end consumer.
Automotive ecosystem partners are working together to develop equitable business models and approaches to alleviate tariff cost impact and reduce the risk to consumers of vehicle price increases and availability declines. These connections and new approaches are particularly important in Japan, where much of the auto supplier base consists of small and medium-sized businesses (SMBs). We have seen, for example, SMBs and large OEMs accelerate vehicle shipments and manufacturing of parts during the 90-day tariff pause which ended on 9 July. Manufacturers tell us that the absence of significant price increases in response to tariffs thus far may be a result of working down older, lower cost inventory. With this strategy, however, comes financial risk and potential cash flow issues (particularly for the small vendors) as tariffs are paid up front in a short period of time. There is also risk across interconnected regions, such as in Asia Pacific: multiple Japanese auto OEMs (Toyota, Honda, Isuzu, Mitsubishi) have big investments in Thailand particularly for electric vehicles (EVs) and the U.S. is Thailand’s top auto export destination (18%).
The on-again/off-again tariff situation makes it extremely challenging for OEMs and suppliers in the industry to properly plan for new R&D and production. Companies are struggling to commit to new US production based on this unpredictability–building new facilities or even reopening and improving shuttered ones is not something that happens quickly. Although it is likely that large auto manufacturers and suppliers that had plans in place for new facilities and/or joint ventures with American companies will accelerate those plans. For example, battery providers such as LG Energy Solution and Panasonic are working with auto EV OEMs such as GM, Ford, Tesla, and Rivian, as well as semiconductor companies such as Qualcomm. GM recently announced a $4B investment in three existing U.S. factories. Automotive production output as of June 2025 is mostly flat everywhere globally, with this expected to continue through CY2027 (source: S&P Global Mobility). Notably, however, as of June 2025, Japan’s manufacturing purchasing managers’ index (PMI) rose to 50.4 from 49.4, after 11 months of contraction (below 50). It remains to be seen whether this will spark consistent growth or is a brief increase in response to the 90-day tariff reprieve.
In IDC’s 2025 Supply Chain Survey, automotive manufacturers identified their top three strategies to mitigate supply chain risks as improving supply chain agility, improving supply chain visibility, and prioritizing local ingredient/component supply (near-shoring) over global sourcing. These priorities underscore a broader industry shift toward localized resilience and faster response capabilities, driven not just by tariffs but by chronic disruptions, digital transformation pressures, and a push for ecosystem alignment.
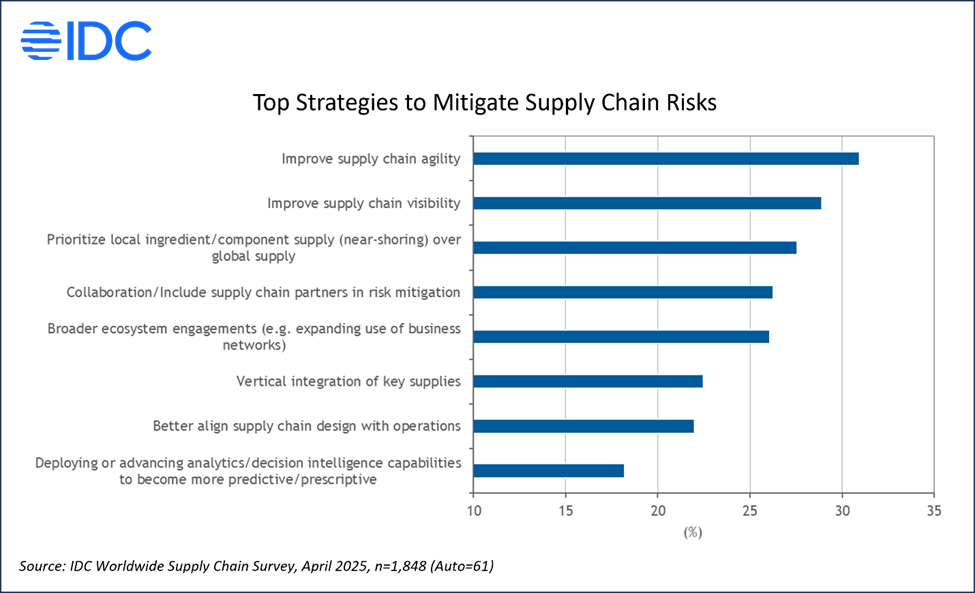
At the same time, the automotive industry continues to face other monumental structural shifts, all of which could be impacted by tariffs: the expansion of software-defined vehicles, the growth of electric vehicles (EVs), and the ongoing digital talent shortages and lack of new workers entering the industry. An upcoming IDC Perspective will expand on these three challenges and opportunities and the related tariff impact.
The ambiguous tariff environment that global automotive OEMs and their suppliers are currently living through may ultimately turn out to be a benefit by forcing continuous collaboration, data sharing, and knowledge visibility, if this is not currently present. Automotive is already an ecosystem-driven industry, with participants from the private and public sectors, multiple tiers of the supply chain, and other industries working closely together. Sharing risk, resources, talent, and data across this ecosystem will enable rapid response to increasing consumer demand for software-rich, electric vehicles, as well as a flexible response to economic and geopolitical disruptions.
Take the next step and discover how IDC’s research can help you with your Supply Chain strategy, implementation, and digital transformation. Contact IDC via this form. For research specific to Industry Ecosystems & Business Networks, please go to this page.