The Asia/Pacific region, which serves as the world’s largest manufacturing and consumer hub, is expected to continue growing despite challenges such as a sluggish global economy, higher interest rates, material cost inflation, and protectionist trade policies.
Governments across the region, including those of China, India, South Korea, Taiwan, Singapore, Malaysia, and Thailand, are actively supporting the manufacturing sector. They are rolling out initiatives to accelerate digital transformation, improve connectivity infrastructure, and promote green economy practices, opening new opportunities for both manufacturers and technology vendors.
Looking at these market dynamics and technology adoption trends in the region, IDC published its FutureScape Worldwide Manufacturing 2025 Predictions – Asia/Pacific (excluding Japan) Implications report to provide organization decision-makers with an actionable investment plan with respect to technologies as viable enablers.
Each prediction is presented based on timeline projection, complexity assessment, and organizational impact. It also includes insights into regional use cases and examples, as well as the regional outlook for manufacturing over the next five years.
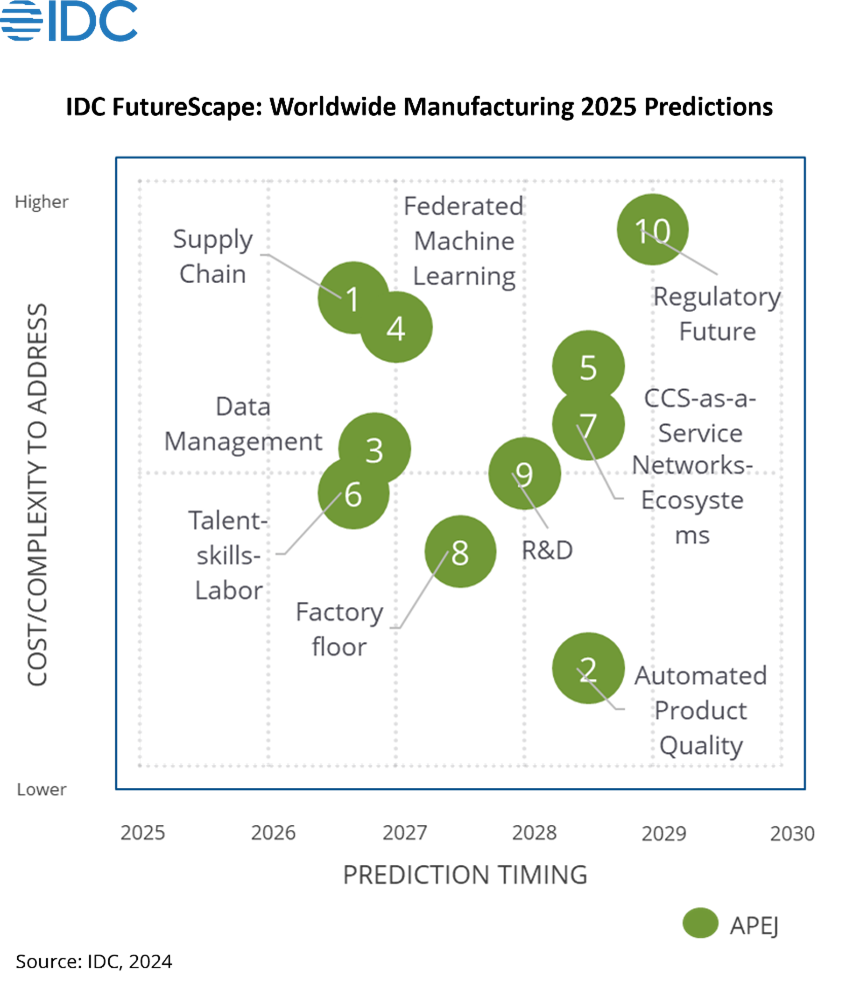
The following are some of the key predictions for Manufacturing in Asia/Pacific (excluding Japan):
AI and Automation: Unleashing Next Level Production Efficiency
Supply chain complexity and competition in Asia are intensifying as manufacturers face mounting cost pressures. The cost of raw materials continues to rise, driven by factors such as global supply constraints, fluctuating commodity prices, and regional demand surges. Shifting customer preferences are leading to shorter lead times and fluctuating order volumes, adding further complexity to an already intricate supply chain.
To overcome these challenges, manufacturers must prioritize flexibility and productivity efficiency to achieve operational excellence and boost their perfect order (PO) rate, a critical metric for fulfilment success.
This sparks a renewed interest in adopting technology solutions to integrate production process with supply chain management. According to IDC’s Manufacturing Industry Core Survey, July 2024; 30% of APAC manufacturers responded that advanced planning and scheduling (APS) solutions significantly contribute to helping their organizations achieve operational KPIs. AI/GenAI, can significantly enhance performance and integration between different systems and processes.
As a result, IDC predicts that by 2027, resiliency pressures and AI opportunities will drive more than 30% of Asia-based Top 2000 (A2000) manufacturers to invest in new advanced planning & scheduling deployments, leading to PO rates of above 95%.
The Intersection of Complexity and Quality in Modern Manufacturing
Ensuring impeccable product quality is a constant pursuit for manufacturers, demanding constant vigilance and adaptation. The growing complexity of manufacturing processes and materials has resulted in the emergence of a new set of challenges. The rapidly growing variety of potential defects, coupled with limitations of real-world testing data, can impede the effectiveness of conventional inspection systems. These limitations can lead to missed defects, ultimately impacting product quality, consumer trust and may cause the potential risk of regulatory violation.
GenAI can improve quality initiatives in multiple ways. GenAI can significantly streamline data management by efficiently collecting, organizing, and summarizing vast amounts of structured and unstructured data from diverse sources, including design, manufacturing, supply chain, distribution, customer feedback, and service support. This centralized data repository enables AI-powered analysis to identify potential risks, inform decision-making, and optimize processes.
Additionally, through synthetic data augmentation, GenAI can facilitate comprehensive and accurate simulations, aligning product development with stringent requirements and customer preferences simultaneously saving time and resources. As a result, IDC also predicts that by 2028, 40% of APeJ manufacturers will be leveraging GenAI to automate product quality management and improve development time/cost by 10%.
For example, Bosch, a renowned industry leader, has already successfully implemented AI-powered image recognition for quality control. However, given their already high manufacturing standards, acquiring sufficient data on product defects to train their AI system proved challenging. To overcome this limitation, Bosch turned to GenAI, which enabled them to create a vast dataset of synthetic defect images from a relatively small number of real-world examples. This innovative approach accelerated the training of their automated optical inspection systems, allowing for earlier detection of potential issues in the production process.
Leveraging Ecosystem Alliances for Sustainable Growth
Fluctuating market demands and geopolitical tensions, has led to significant disruptions in raw material supply chains. Rising logistics costs and workforce shortage further cause costs and productivity challenges. Manufacturers across the region are compelled to re-evaluate and adapt their supply chain strategies to ensure business continuity. In this context, supply chain reliability has emerged as a critical competitive differentiator, particularly for industries reliant on timely service parts delivery.
Customers today demand high levels of uptime and efficient support, as outlined in their Service Level Agreements (SLAs). Delays in procuring necessary parts can lead to costly operational disruptions. To meet these stringent expectations, manufacturers are expanding their spare parts ecosystems. By ensuring a ready supply of critical components, manufacturers can expedite repairs, minimize downtime, and ultimately enhance customer satisfaction. Customers now seek proactive service, not just reactive repairs. They desire assurance that their equipment will be serviced promptly, enabling continuous operations and reducing risks.
As a result, IDC predicts that, because manufacturers are unable to meet global repair SLAs, by 2028, 40% of A2000 manufacturers will expand its spare parts ecosystem partners across the supply chain to confidently deliver resolution and customer outcomes.
For example, Samsung Electronics has launched an online Supplier Portal to attract potential new suppliers, aiming to strengthen its supply chain and mitigate associated risks. Samsung’s dedicated internal team, the International Procurement Center, operates as the central procurement hub, tasked with identifying top-tier suppliers in strategically important regions across the globe.
Expanding the spare parts ecosystem provides opportunities for revenue growth, as companies can offer premium support packages with prioritized service levels, attracting customers who value reliability. This approach strengthens customer relationships, builds loyalty, and differentiates the manufacturer from competitors by ensuring high standards of service and reduced equipment downtime.
Call for Actions:
- Conduct a thorough assessment of business and operational points and develop a phased automation strategy that aligns GenAI/AI investments with business priorities for maximum impact.
- Organizations need to evaluate their existing technology infrastructure and identify connectivity gaps to build connected ecosystems to increase process visibility and ensure interoperability and compatibility for successful deployment. It is important to choose the right architecture (on-premises or cloud-based) and data platform that aligns with their specific requirements and have scalability in mind.
- Establish a cross-functional data governance team to define data quality standards, implement automated data cleaning pipelines, and enforce strict validation checkpoints at data entry, integration, and model input stages, ensuring AI and GenAI models consistently receive high-integrity data for optimal decision accuracy.
- Strategized and establish a robust data governance framework. Consider implementing a centralized data management platform with strict access controls and data privacy policies. Periodically conduct regular data quality checks and audits to review performance and monitor benefits and outcomes from the initiative.
To learn more about IDC’s top 10 predictions for the Asia/Pacific (excluding Japan) Manufacturing Industry, click here. For specific recommendations for tech vendor sales and marketing leaders to understand clients’ priorities and enhance their storytelling and go to market plans, click here.
Get a better understanding of the foundations for advanced AI-driven capabilities to build a future-ready supply chain, attend this on-demand webinar.